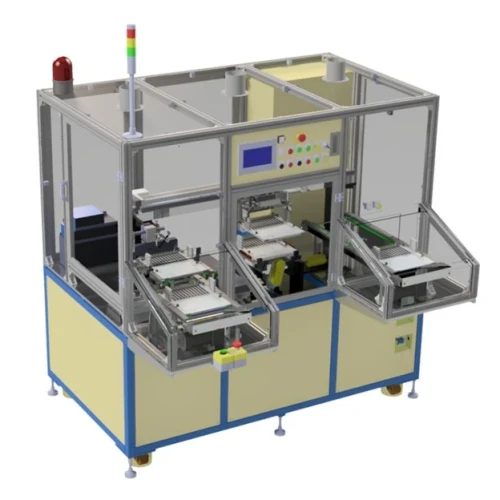
Máy nhúng thiếc
The automatic tin dipping machine is a specialized automated device used to dip electronic products into molten tin before moving on to the next step in the assembly line. The system is custom-designed according to the production line layout and specific product requirements from each customer.
Tin dipping is a crucial technology in the electronics industry, offering many advantages such as automation, high soldering quality, production efficiency, and tin savings. However, certain limitations should also be considered, including initial cost, system complexity, and limited adjustability.
VIETNAM CNC & TECHNOLOGY APPLICATION JOINT STOCK COMPANY
Hotline: +84.916 63 9355 / +84.915 74 4664
Email: Sales01@cncvina.com.vn / Sales03@cncvina.com.vn
Product description
Introduction to the tinning machine
The automatic tinning machine is a specialized automated device used to dip electronic components into molten solder before moving on to subsequent stages in the assembly line. The system is custom-designed to suit the specific production line and the requirements of each customer for their particular products.
Definition and working principle of the tinning machine
A tinning machine is defined as a device used in the process of melting and applying tin to create an electrical connection.
The working principle of the machine is based on melting solder to form reliable contact points on the surfaces of electronic components. Accurate control of temperature and melting time is critical to ensure the quality and durability of the connections.
Historical background and development of assembly lines
The development of tinning machines began in the 1960s, alongside the rapid growth of the electronics industry and the increasing demand for high-quality electrical connections. Since then, manufacturers have continuously upgraded and refined tinning machines to meet the ever-evolving needs of the market. Thanks to this ongoing advancement, modern tinning machines have become more sophisticated and flexible in electronic component production.
Key features of the tinning machine
Precise temperature control
-
Adjustable temperature: The machine allows for precise temperature adjustment to ensure optimal soldering conditions and prevent component damage.
-
Temperature stability: Advanced temperature control systems maintain stable heat throughout the soldering process for consistent results.
Automation and programming
-
Automatic soldering programs: Modern tinning machines come equipped with pre-programmed soldering cycles, enabling the execution of complex processes without manual intervention.
-
Flexible programming: Users can program various soldering parameters according to the type of components and circuit boards being processed.
Automatic solder feeding system
-
Consistent solder supply: The automatic pump system ensures a steady and accurate delivery of solder to the soldering area.
-
Solder quantity control: Adjustable solder flow prevents over- or under-soldering during the process.
Automatic cleaning system
-
Soldering tip cleaning: Some tinning machines are equipped with automatic tip cleaning systems to maintain high soldering performance and extend the lifespan of soldering heads.
-
Residue removal: The cleaning system effectively eliminates solder residue and other contaminants from the soldering tip.
High precision and uniform soldering
-
Precision soldering heads: Designed with high precision to ensure uniform and accurate soldering at even the smallest and most complex solder points.
-
Accurate movement: Integrated mechanical and electronic systems guarantee precise motion of the soldering head to the correct soldering locations.
Safety features
-
Overheat protection: Prevents abnormal temperature rises, ensuring the safety of both the equipment and the operator.
-
Anti-static protection: The machine is often equipped with anti-static features to protect sensitive components from electrostatic discharge (ESD).
Monitoring and error detection system
-
Soldering process monitoring: The system continuously monitors all process parameters to ensure they remain within acceptable limits.
-
Error alerts: The machine can detect faults and issue alerts, allowing operators to quickly identify and resolve problems.
Connectivity and integration capabilities
-
Computer connectivity: Some models support PC connectivity for process management, soldering data storage, and detailed reporting.
-
Integration with other equipment: The machine can be integrated with other production systems such as wave soldering machines, automated optical inspection (AOI) equipment, and functional testing systems.
High performance and durability
-
High-quality materials: Constructed from heat-resistant, durable materials that ensure long service life.
-
Robust design: Engineered for reliability and stability, allowing continuous operation in harsh industrial environments.
Applications of solder dipping machines
In the manufacturing industry
Electronics manufacturing:
-
Printed circuit board (PCB) assembly: Solder dipping machines are used to solder electronic components onto PCBs, ensuring both electrical and mechanical connections between components and circuits.
-
Consumer electronics production: Products such as mobile phones, tablets, and other electronic devices use solder dipping technology in their manufacturing process.
Industrial equipment manufacturing
- Automation equipment: Automated control systems and industrial robots commonly utilize printed circuit boards (PCBs) and components soldered using tin dipping machines.
- Telecommunication devices: Tin dipping machines assist in soldering critical components in telecommunication devices, ensuring system performance and reliability.
Consumer goods manufacturing
Smart home appliances: Devices like smart washing machines and refrigerators use PCBs and electronic components soldered with tin dipping technology.
In medicine and biology
Medical equipment
- Heart rate monitors, hearing aids: These medical devices require high-quality solder joints to ensure accuracy and reliability.
- Biosensors: Tin dipping machines are used to solder biosensors onto PCBs, facilitating the measurement of biological parameters such as glucose, heart rate, and chemical substances in the body.
Biotechnology
- DNA and RNA analysis devices: These devices often require electronic components soldered by tin dipping machines to operate accurately and efficiently.
- In vitro diagnostic (IVD) equipment: Tin dipping machines help create complex electronic circuits necessary for IVD devices used in disease diagnostics.
Applications in biological research
Development of research equipment: Advanced biological research devices, such as PCR (Polymerase Chain Reaction) machines and centrifuges, utilize PCBs and components soldered by tin dipping machines.
In research and development
Development of new electronic products
- Prototyping: Researchers and engineers use tin dipping machines to quickly prototype new circuit designs.
- Testing and adjustment: Tin dipping technology allows for necessary testing and adjustments during the development of electronic products.
Materials technology research
Development of new tin alloys: Scientists research and develop tin alloys with improved features, such as higher mechanical strength or better corrosion resistance.
Research in soldering technology
Process improvement: Exploring and developing new soldering techniques to enhance the efficiency and quality of the soldering process.
Types of tin dipping machines
Manual tin dipping machines
Manual tin dipping machines are the most basic type of soldering equipment, commonly used in applications requiring flexibility and human intervention.
Soldering Iron
-
The primary tool used in manual tin dipping machines.
-
Typically features a corrosion-resistant tip with good thermal conductivity.
-
Temperature adjustments are made to suit different components and PCBs.
PCBs and components
-
Components are placed on the PCB according to specified designs.
-
Components and PCBs are secured on the workbench of the tin dipping machine.
Solder and flux
-
Solder and flux are usually prepared in advance.
-
Solder melts and creates a bond between the component and the PCB.
Soldering operation
-
The user controls the soldering iron to apply heat to the soldering areas.
-
Solder is applied to the soldering area, forming a joint upon contact with the component and PCB.
Inspection and repair
-
After soldering, the PCB is inspected to ensure joints are uniform and secure.
-
Repairs or adjustments are made if necessary.
Advantages of manual tin dipping machines
-
Flexibility: Allows for intervention and adjustments based on specific job requirements.
-
Suitable for small-scale production or component repair.
Limitations of manual tin dipping machines
-
Speed: Generally inefficient for large-scale mass production processes.
-
Precision: May not ensure high precision like automated machines.
Manual tin dipping machines are suitable for tasks requiring human intervention and flexibility, especially in small-scale or personal applications. However, to optimize efficiency and quality, manufacturing companies often transition to automated tin dipping machines for large-scale mass production.
Semi-automatic tin dipping machines
Semi-automatic tin dipping machines are an ideal choice between full automation and human intervention.
Features
Automation
-
Designed to perform soldering processes automatically without human intervention.
-
Automated control systems are programmed to execute specific soldering processes reliably and consistently.
Pre-programmed soldering processes
-
Capable of pre-programming specific soldering processes based on production requirements.
-
Can program timing, temperature, pressure, and other parameters for each soldering process.
Mobile workbench
-
Often equipped with a mobile workbench or conveyor belt to move PCBs through soldering positions.
-
The mobile workbench optimizes the production process and enhances efficiency.
Automatic solder pumping system
-
Features an automatic solder pumping system to deliver solder to soldering points accurately and evenly.
-
Ensures quality solder joints without excess solder.
Temperature control
Equipped with precise temperature control systems to ensure soldering occurs at the correct temperature.
Cleaning system
-
May include automatic cleaning systems to maintain cleanliness and reliability of soldering tips.
-
Helps remove any solder residue or impurities that could affect joint quality.
Applications
Mass production
-
Suitable for large-scale mass production processes.
-
Provides automation for soldering multiple joints simultaneously, minimizing human intervention and enhancing production efficiency.
Research and development
Used in laboratories and research centers to conduct automated soldering experiments and studies.
Industrial applications
Employed in manufacturing electronic products like mobile phones, computers, control panels, and other consumer electronics.
The semi-automatic solder dip machine is an essential tool in the electronics industry and in research and development. By combining automation with human intervention, semi-automatic solder dip machines help optimize the production process and ensure the quality of the final product.
Automatic solder dip machine
The automatic solder dip machine is a fully automated solution for the soldering process on printed circuit boards (PCBs). Below are some details about automatic solder dip machines:
Features
Fully automated operation
- Automatic solder dip machines operate completely without human intervention during the soldering process.
- The automated control system is programmed to execute the entire soldering sequence reliably and consistently.
Pre-programmed settings
- Soldering processes are pre-programmed and easily adjusted based on the specific requirements of each production application.
- You can configure timing, temperature, pressure, and other parameters for each soldering task.
Automatic conveyor system
- Usually equipped with an automatic conveyor to move PCBs through different soldering positions on the production line.
- The conveyor system helps optimize workflow and boost productivity.
Automatic solder pump system
- An automatic solder pump precisely and evenly delivers solder to each joint.
- This ensures consistent quality and prevents excess solder at the joints.
Temperature and time control
Automatic solder dip machines are equipped with precise control systems for temperature and time to ensure the soldering process occurs under optimal conditions.
Automatic cleaning system
- Often equipped with automatic cleaning systems to maintain cleanliness and reliability of the soldering tips.
- These systems help remove any solder residue or impurities that could affect joint quality.
Applications
Mass production
- Automatic solder dip machines are ideal for large-scale mass production.
- They automate the soldering of multiple joints simultaneously, minimizing human intervention and increasing productivity.
Research and development
These machines are also used in laboratories and R&D centers to carry out experiments and research on automated soldering.
Industrial applications
Used in manufacturing of electronics such as mobile phones, computers, control panels, and other consumer electronics.
Advantages and limitations of solder dip machines
Advantages
-
Automation: Solder dip machines automate the soldering process, reducing reliance on manual labor and enhancing production efficiency.
-
High-quality joints: With precise control of temperature and time, the machines produce consistent and high-quality solder joints on PCBs.
-
Flexibility: Can be programmed to handle different types of solder joints depending on specific product requirements.
-
High throughput: Capable of performing hundreds or even thousands of solder joints per hour, greatly improving production capacity.
-
Solder savings: The automatic solder pump system helps reduce solder waste by accurately dispensing solder only where needed.
Limitations
-
High initial cost: Solder dip machines typically require a higher initial investment compared to manual soldering methods.
-
Complexity: Installation and operation may require advanced technical knowledge and staff training.
-
Limited adjustability: Some machines have limited capabilities in adjusting soldering parameters, especially fixed-type machines.
-
Complex maintenance and repairs: Maintenance and repairs can be complicated and require experienced technicians.
-
Limited applicability: Not suitable for all soldering applications, especially where flexible human intervention or highly customized soldering is required.
Conclusion
The solder dip machine is a vital technology in the electronics industry, offering benefits such as automation, high-quality joints, increased production efficiency, and solder savings. However, considerations such as high initial cost, complexity, and limited adjustability should be taken into account.
The integration of Artificial Intelligence (AI) and the Internet of Things (IoT) can enhance data analysis and optimize the soldering process—from predicting and preventing errors to boosting efficiency and energy savings.
The advancement of robotics and full automation can further streamline the operation of solder dip machines, from component placement to final product inspection and packaging.
Soldering technology continues to evolve toward creating stronger, more precise, and consistent joints while minimizing environmental and health impacts.
Incorporating green and sustainable technologies into solder dip machine production can help reduce waste and resource consumption, while improving the overall sustainability of the electronics industry.