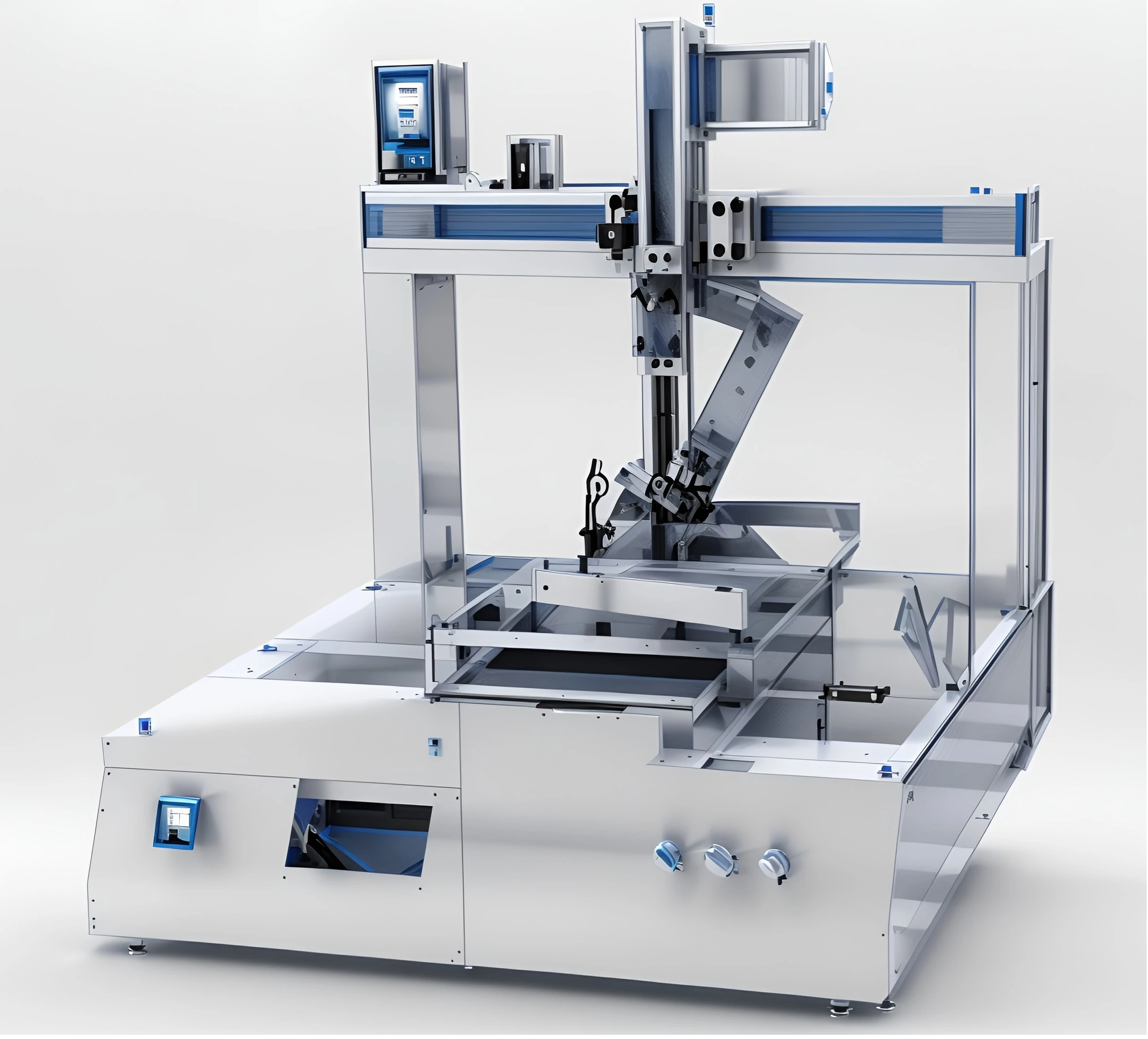
3-axis PCB soldering robot
The 3-axis desktop soldering robot is a robotic system designed to automate the process of soldering electronic components onto circuit boards or other electronic assemblies. It is applied in mass production environments.
Desktop soldering robots are commonly used in electronic manufacturing and assembly processes to increase efficiency, improve product quality, and reduce production costs.
VIETNAM CNC & TECHNOLOGY APPLICATION JOINT STOCK COMPANY
Hotline: +84.916 63 9355 / +84.915 74 4664
Email: Sales01@cncvina.com.vn / Sales03@cncvina.com.vn
Product description
3-Axis PCB soldering robot
The automatic PCB soldering machine is an advanced automated device used in the electronics manufacturing industry to solder electronic components onto printed circuit boards (PCBs) without manual intervention. These machines enhance efficiency, precision, and consistency in the soldering process, making them essential for high-volume production and complex PCB assembly.
Importance of using an automatic PCB soldering machine
PCB soldering machines are indispensable in the manufacturing of electronic devices. Their ability to solder components onto PCBs accurately, efficiently, and consistently ensures the production of high-quality, reliable electronic products.
By automating the soldering process, these machines significantly improve production efficiency, reduce costs, and enhance the overall quality of electronic assemblies, making them vital in the industry.
Functions of the PCB soldering machine
Key components
-
Robotic arm: Equipped with precision motion controls to accurately pick and place components on the PCB.
-
Vision system: Cameras and image processing software ensure correct alignment and placement of components.
-
Feeder system: Supplies components to the robotic arm for placement.
-
Welding system
Reflow Oven
-
Preheat zone: Gradually increases PCB temperature to activate flux and reduce thermal shock.
-
Soak zone: Maintains a steady temperature to ensure uniform heating.
-
Reflow zone: Heats the PCB to the solder’s melting point to form solid joints.
-
Cooling zone: Gradually cools the PCB to solidify the solder.
Temperature control system
Thermocouples and sensors: Monitor temperature at various stages.
Conveyor system
Transport mechanism: Moves the PCB through different stages of the soldering process.
Inspection and quality control system
-
Automated optical inspection (AOI): Uses high-resolution cameras to detect solder joint defects.
-
X-ray inspection: Detects hidden joints, such as those in BGA components.
-
Data logging and analysis: Records soldering parameters and inspection results for quality control.
How the PCB soldering machine work?
The PCB is loaded onto the conveyor system. Components are supplied to the placement head through feeders. Alignment and positioning: The vision system and robotic arm work together to precisely place components on the PCB.
Welding process:
-
Preheating: The PCB enters the preheating zone of the reflow oven, where it is gradually warmed up.
-
Soaking: The PCB moves to the soaking zone for even heating.
-
Reflow: The PCB reaches the reflow zone, where the solder melts and forms joints.
-
Cooling: The PCB is cooled down to solidify the solder joints.
Inspection and quality control:
-
AOI and X-ray inspection: The PCB undergoes inspection to detect any soldering defects.
-
Data analysis: Inspection data is analyzed, and defective boards are identified for rework if necessary.
- Finished PCB: Completed and inspected PCBs are unloaded from the conveyor system.
Key features of the 3-axis PCB soldering robot
High speed and precision
The flexible 3-axis robotic soldering arm can be programmed for precise movements at speeds up to 50 mm/s.
Stable and consistent soldering quality
The intelligent control system ensures accurate temperature regulation, improving and stabilizing solder joint quality.
User-friendly interface and easy programming
The simple interface allows operators to easily modify soldering programs and switch between automatic and manual modes to suit actual conditions.
Smart camera system
- Equipped with an integrated AI camera system for PCB alignment recognition and fast, accurate defect detection.
- Environmental and operator safety
- The solder fume extraction system protects both the operator and the surrounding environment.
Thông số kỹ thuật Robot hàn 3 trục mạch in
Machine dimensions | 930x650x880 mm, 80kg |
Working area | 550x300x100 mm |
Solder wire diameter | D6 - D12 |
Temperature control range | 0-500°C (±1°C) |
Air pressure | 0.4-0.6 MPa |
Welding method | Point soldering / Drag soldering |
Tip cleaning | Pneumatic cleaning |
Number of soldering heads | 1-2 heads (customizable) |
Repeatability accuracy | ±0.02 mm |
Types of PCB soldering machines
Reflow soldering machine
Reflow oven: The most commonly used equipment in PCB manufacturing, the reflow oven performs soldering by moving the PCB through various thermal zones to melt and solidify solder.
Main components:
- Preheat zone: Gradually heats the PCB to avoid thermal shock.
- Soak zone: Maintains a stable temperature to ensure even solder melting.
- Reflow zone: Reaches peak temperature to fully melt the solder.
- Cooling zone: Cools the PCB to solidify the solder joints.
Wave soldering machine
Conventional wave soldering: Used primarily for PCBs with many through-hole components.
Main components:
- Solder pot: Holds molten solder.
- Solder wave pump: Creates a wave of solder to contact the PCB.
- Fluxing system: Applies flux to clean and protect soldering surfaces.
- Preheating zone: Warms the PCB before wave soldering.
- Cooling zone: Cools the PCB after soldering.
Selective soldering machine
Selective soldering pot: Uses a small solder pot to solder specific areas of the PCB.
Mini-wave soldering: Uses a solder nozzle to precisely solder selected areas.
Main components:
- Fluxing system: Applies flux only to areas that require soldering.
- Soldering head: Solder nozzle or mini pot, movable to target specific joints.
- Movement system: Robot or mechanical positioning system for precise head placement.
Robotic soldering machine
Fully automated robotic soldering: These systems use robots equipped with soldering heads to perform soldering processes with extremely high precision.
Key components include:
- Robotic arm: Precisely controls movement.
- Soldering head: Includes thermal soldering, laser soldering, or mini wave soldering.
- Vision system: Utilizes cameras and image processing software for positioning and inspection of the soldering process.
Laser soldering machine
Direct laser soldering: Uses a laser beam to melt solder, creating highly accurate joints with minimal thermal impact on surrounding areas.
Key components include:
- Laser source: Generates a laser beam with suitable power and wavelength.
- Movement system: Accurately positions the laser beam on the PCB.
Ultrasonic soldering machine
Contactless soldering: Utilizes ultrasonic waves to melt and distribute solder without direct contact with the PCB surface.
Key components include:
- Ultrasonic transducer: Generates ultrasonic waves to melt solder.
- Control system: Ensures appropriate frequency and intensity of the ultrasonic waves.
Benefits of using automated PCB soldering machines
Increased efficiency and productivity
-
Automated machines can process large volumes of PCBs in a shorter time than manual soldering, significantly increasing production speed.
-
These machines can operate continuously with minimal downtime, further enhancing productivity.
-
They can handle various PCB designs, sizes, and component types, enabling manufacturers to adapt easily to different product requirements.
Enhanced precision and accuracy
Automated soldering ensures uniform joints, reducing variability and defects common in manual processes.
-
Accurate component placement: Advanced vision systems and robotic arms allow for precise alignment and placement, crucial for high-density PCBs.
-
Reliable solder joints: Controlled processes result in strong, dependable joints essential for electronic performance and durability.
-
Integrated inspection: Automated Optical Inspection (AOI) and X-ray inspection systems detect defects early, ensuring high-quality output and minimizing field failure risks.
Cost-effectiveness
-
Automation reduces the need for skilled labor, lowering overall production costs.
-
Minimized rework and waste: Consistent quality and defect detection reduce the need for rework and scrap, saving materials and labor.
Reduced human error
-
Automatic precision: Automation eliminates inconsistencies and errors associated with manual soldering, resulting in higher accuracy and fewer mistakes.
-
Consistent process execution: Machines follow exact programs and settings, ensuring consistent soldering procedures.
Applications of PCB soldering machines
Automated PCB soldering machines are widely used across multiple industries due to their ability to perform precise, consistent, and high-quality soldering, making them indispensable in modern electronics manufacturing.
Consumer electronics
-
Smart devices production: Used for soldering compact, densely packed parts in High-Density Interconnect (HDI) PCBs for smartphones, tablets, and other smart devices.
-
Home appliances: Automation ensures reliable joints in complex PCBs used in TVs, refrigerators, and washing machines.
Industrial equipment & automation
-
Control systems: PCBs in industrial controllers and PLCs require reliable solder joints for accurate and consistent performance.
-
Robotics: High-precision soldering is essential for PCBs in robotic arms and automation systems used in production and assembly lines.
-
Sensors and actuators: Automated soldering machines assemble PCBs in various sensors and actuators used in industrial applications.
Telecommunications
-
Mobile network infrastructure: Used for soldering PCBs in base stations, repeaters, and other critical telecom infrastructure.
-
Satellite communication: Ensures reliable soldering of components in satellite communication equipment and ground stations.
Aerospace and defense
-
Avionics systems: High-reliability joints are crucial for performance and safety in avionics systems used on aircraft.
-
Defense equipment: Automated machines ensure PCB reliability in military communication systems, radar systems, and other defense electronics.
Future trends and innovations in PCB soldering machines
The future of automatic PCB soldering machines is shaped by advancements in technology and growing demands in the electronics manufacturing sector. Key trends and innovations include:
Automation and artificial intelligence (AI)
- AI and machine learning applications: Improve the accuracy and efficiency of soldering processes. These systems learn from production data to optimize soldering parameters, reduce errors, and enhance product quality.
- Predictive analytics: Use AI to analyze production data to predict and prevent soldering defects before they occur.
Enhanced connectivity and IoT (Internet of things)
-
Automated soldering machines will be connected to networks for remote monitoring and management. This allows manufacturers to easily track machine performance and perform preventive maintenance.
-
IoT in smart manufacturing: Connect soldering machines to smart manufacturing systems to optimize the entire production process.
Advanced soldering technologies
-
Laser soldering: Gaining popularity due to its precision and minimal thermal impact on surrounding components.
-
Contactless soldering: Using techniques like ultrasonic waves to solder without direct PCB contact, reducing damage risk and improving accuracy.
Improved quality control
Automated Inspection Systems: Integration of AOI and X-ray systems ensures real-time quality monitoring of solder joints.
Intelligent fault diagnosis: Algorithms are used to detect and diagnose complex soldering defects during production.
Integration with emerging manufacturing technologies
-
3D printing and PCB soldering: Combine 3D printing with PCB soldering to create complex PCB structures with greater functionality.
-
Microsoldering: Development of microsoldering techniques for handling increasingly compact and complex electronic components and circuits.
Applications in new fields
-
Medical and healthcare devices: Increased accuracy and reliability in PCB soldering to meet stringent requirements in medical equipment production.
-
Green technology: Development of PCB soldering applications in renewable energy devices such as solar panels and wind energy systems.
Kết luận
Automated Printed Circuit Board (PCB) soldering machines are an essential part of modern electronics manufacturing. They play a key role in ensuring precise, consistent, and high-quality solder joints, thereby improving the performance and reliability of electronic products. These machines save time and reduce human errors, meeting the increasing demands for efficiency and quality in the electronics industry.
Advancements in automatic PCB soldering technologies not only improve production performance and quality but also help reduce costs and enhance safety. The integration of AI, IoT, and advanced soldering technologies will shape the future of the electronics industry, bringing more innovative and efficient solutions.
For customers interested in automated machines for the electronics assembly industry, please contact:
VIETNAM CNC & TECHNOLOGY APPLICATION JSC.
Factory: Song Cung IDZ, Dong Thap, Dan Phuong, Ha Noi
Phone: +84.916 63 9355 / +84.915 74 4664
Website: https://cncvina.com.vn; https://cncvina.net; https://cncviname.com.vn
Email: sales01@cncvina.com.vn | sales03@cncvina.com.vn