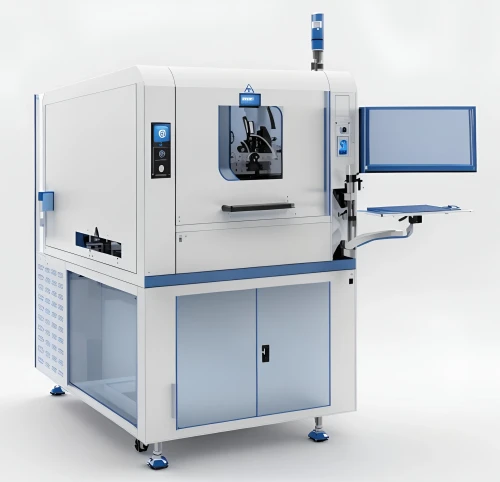
PCB inspection machines
pcb are a crucial part of the PCB manufacturing process. Ideally, testing should be carried out throughout the production cycle to prevent defects in the final product. These tests, conducted on prototypes or small-scale assemblies, focus on detecting short circuits, soldering issues, and functionality problems, ensuring that each tested PCB operates properly.
AOI (Automated Optical Inspection) uses a 2D camera or dual 3D cameras to capture images of the PCB. The system then compares the board images to a detailed schematic. If a board does not match the schematic to a certain degree, it is flagged for further inspection by a technician.
VIETNAM CNC & TECHNOLOGY APPLICATION JOINT STOCK COMPANY
Hotline: +84.916 63 9355 / +84.915 74 4664
Email: Sales01@cncvina.com.vn / Sales03@cncvina.com.vn
Product description
General introduction to the PCB inspection machine
The PCB inspection machine is an Automated Optical Inspection (AOI) system that performs visual inspections of printed circuit boards (PCBs) during the manufacturing process. It uses a camera to scan the PCB in great detail to detect any defects or damages. AOI integrates optics, mechanics, electronic control, and software to replace the human eye. In reality, PCBs are becoming increasingly smaller and more complex; even a relatively simple board can consist of thousands of soldered components. AOI supports monitoring the quality of PCB production and enables in-process repairs, which is a key to success in today’s competitive PCB manufacturing industry.
PCB stands for Printed Circuit Board. It is a substrate used to support and connect electronic components, typically made from one or more layers of non-conductive material (usually fiberglass-reinforced plastic) coated with one or more layers of conductive material (usually copper).
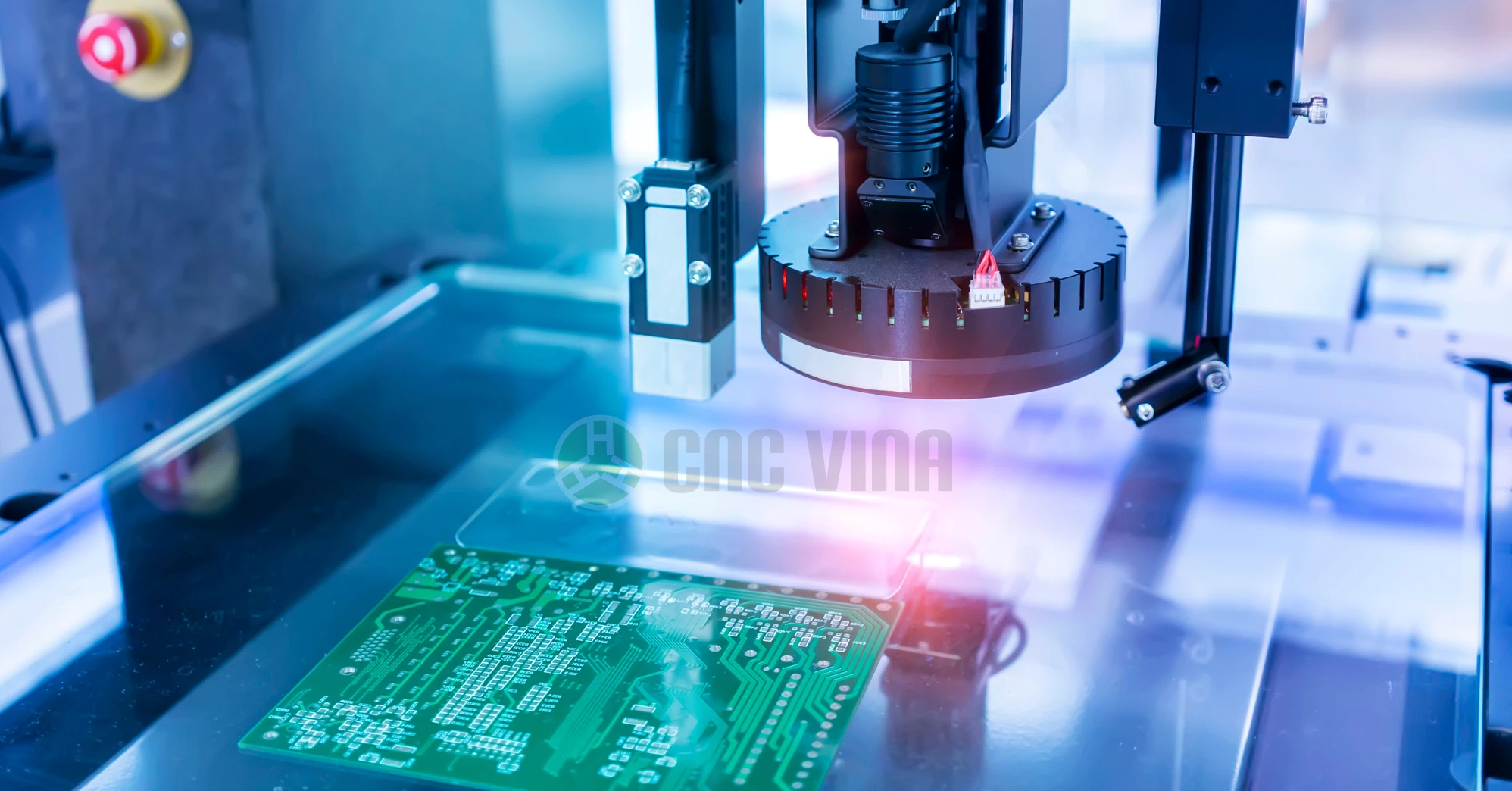
Technical specifications and structure of the PCB inspection machine
Technical specifications
Dimensions | L1200 x W1000 x H1800 mm |
Power | 2kW |
Power supply | Single - phase 220V - 50Hz |
Control voltage | DC 24V |
Air supply Requirement | 0.4 -0.6 MPa |
Model | HV, GAS |
Max PCB size | L250 x W120 x H3 mm |
Cycle time | 5 - 14 seconds |
Main components
-
Load/Unload conveyor: Responsible for transferring PCBs into and out of the inspection machine. The conveyor can be automatically adjusted to fit various PCB sizes.
-
Fixing jig: Holds the PCB in the correct position to ensure accurate scanning by the camera.
-
Inspection camera system: AOI software processes images, analyzes data, and produces inspection results. This software can be fine-tuned to detect errors and inaccuracies on the PCB.
-
OK/NG sorting tray: Sorts defective (NG) boards for technician review and handling.
-
Sensor system: Sensors are used to determine the position and movement of the PCB during inspection.
-
Lighting system: Provides optimal lighting conditions for the camera to identify details on the board.
Advantages of PCB inspection machines
Ensures that PCB production meets technical specifications, guaranteeing quality and performance. This is critical for safety and reliability across industries like automotive, aerospace, and medical equipment.
Other PCB inspection methods
PCB inspection involves a systematic approach to examining different aspects of their design and functionality. The essential steps include:
Visual Inspection
Begins with checking for physical defects such as soldering issues, corrosion, or damaged components. Ensures all parts are correctly placed and soldered.
Visual inspection
A multimeter is used to check continuity, shorts, and proper voltage levels at various points on the PCB, helping identify individual component or connection issues.Kiểm tra X-quang
Uses advanced X-ray technology to visualize hidden defects inside the PCB. Allows inspection of solder joints, internal traces, and component integrity without damaging the board. Especially useful for complex PCB designs with fine-pitch components and multilayer boards, notably in BGA packages used for advanced ICs like FPGAs.
In-circuit testing (ICT)
Tests the PCB while powered and operational. Test probes and dedicated software assess the correct functionality of components like resistors, capacitors, and ICs.
Functional testing
Involves testing the entire PCB to ensure it meets performance requirements, including I/O ports, power consumption, and communication interfaces.
Burn-In testing
To verify reliability, PCBs are subjected to accelerated operating conditions over extended periods to uncover potential thermal stress-related failures.
The specific inspection methods vary depending on PCB complexity and end-product requirements. Adhering to industry standards and best practices is essential to ensure PCB quality and reliability.
Khách hàng có nhu cầu về các máy tự động phục vụ vui lòng liên hệ:
CÔNG TY CỔ PHẦN ỨNG DỤNG CÔNG NGHỆ & CNC VIỆT NAM
Nhà máy: Điểm công nghiệp Sông Cùng, xã Đồng Tháp, Huyện Đan Phượng, Tp. Hà Nội, Việt Nam
Điện thoại: +84.916 63 9355 / +84.915 74 4664
Website: https://cncvina.com.vn; https://cncvina.net; https://cncviname.com.vn
Email: Sales01@cncvina.com.vn